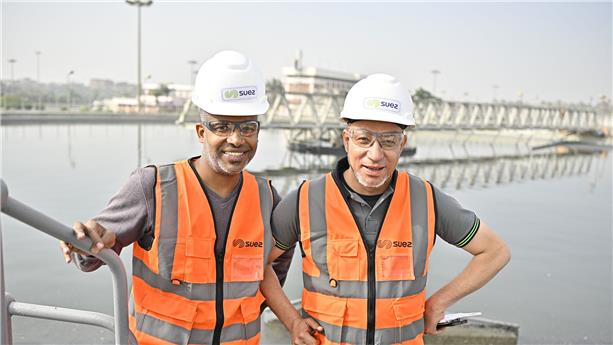
In France, the amount of waste produced across all sectors (agricultural, industrial, tertiary, household and construction) was 345 million tonnes in 2022. This waste is a challenge for local authorities and manufacturers, which have the responsibility of processing it to limit its impact on the environment. However, the waste also constitutes a source of materials that can be recycled into secondary materials or converted into energy.
We work every day to change how people perceive waste, from mere refuse to resources that can be transformed and reused. The group applies a hierarchy of processing methods in its waste management strategy, working with clients to reduce, reuse and recycle waste and recover materials and energy, in order to extract as much value as possible from it.
With 7 million tonnes of waste processed in energy recovery units (ERUs) in France and the UK, SUEZ is a major player in managing waste and converting it into low-carbon resources, in Europe and worldwide. In France and the UK, the group operates 43 ERUs that together produce 2,500 GWh of electricity and 3,000 GWh of heat each year.
The group is continuing to invest in R&D – increasing its spending by 50% since 2022 – to develop new recovery solutions that maximise the amount of material and energy recovered from waste.
Our innovation in action
Three years ago, SUEZ launched its Qualiwaste solution: its aim is to characterise waste, in particular using artificial intelligence technology. SUEZ installs these waste recognition technologies in equipment where it can have the greatest impact: collection centres, sorting centres and energy recovery units. The aim is to help local authorities, individuals and companies with their waste sorting efforts.
Sorting consumer waste more effectively
The Qualiwaste Collecte solution has been fitted to more than 40 refuse trucks in partnership with Lixo and Ficha, making it possible to identify the collection areas where the most sorting errors occur. As a result, local authorities can focus their prevention efforts on those areas and help people to sort their waste more effectively.
Improving the performance of sorting centres
The Qualiwaste Tri solution, developed in partnership with Altaroad, improves the quality of waste entering business waste sorting centres. Cameras are installed at the entrance of centres to carry out an initial check of the waste carried by dump trucks. A second analysis is carried out in the sorting zone to quantify and identify waste suitable for recovery, along with prohibited waste. Qualiwaste Tri has increased sorting performance by 20% at the business waste centre in Cheviré (Loire-Atlantique), the first site to test the technology.
+ 20%
Improving quality control for waste entering ERUs
An experiment is also underway in energy recovery units (ERUs) to identify, using image recognition technology, non-conforming waste and waste suitable for recovery in household waste. The technology detects two types of non-conformity: differences between the type of waste declared beforehand by the company responsible for collection and the type actually received on site, along with the presence of waste that could block the incinerator, such as bulky items.
Limiting the risk of explosion related to nitrous oxide
Finally, SUEZ uses Qualiwaste Nitrous Oxide, a solution developed with the Greater Avignon region in the sorting centre of the SIDOMRA environmental hub. The aim is to address the problem of nitrous oxide bottles at the regional level. The initiative looks beyond the sorting centre, seeking to prevent and find uses for waste, as well as protecting the health and safety of operators and equipment.
“France’s AGEC act means that we must meet ambitious targets regarding waste management. To achieve them, innovation is essential. That’s why we developed Qualiwaste® Tri, an AI-based waste characterisation solution. This leading-edge technology helps us improve our operational efficiency and ensure a safer working environment for our teams. The adoption of Qualiwaste® Tri is an important milestone in the modernisation of our sorting centres. The plan is to apply it on an industrial scale, rolling it out to 10 new sites in 2025 and in a further 30 in future.”
Laurent Carrot, Head of the Business division for waste activities in France
—
Anaerobic digesters are an effective way of managing and processing organic waste, which comes from farms, food producers, parks, gardens and wastewater treatment plants. They stabilise the waste while producing local renewable energy in the form of biogas, as well as digestate that is used in farming as a soil amendment and a substitute for chemical fertilisers.
With 40 years of experience in designing, building and operating anaerobic digesters and biogas recovery units, SUEZ is making significant investments in this industry, which helps to create local loops and supports communities with the energy transition. Worldwide, the Group has built 200 anaerobic digesters and in 2024 operated 50 of them, producing around 500 GWh of non- fossil energy in the form of electricity, heat and biomethane injected into natural gas networks or compressed into biofuel.
Our innovation in action
500 GWh
Limiting the physical footprint of anaerobic digesters
Making waste processing facilities more compact is an area in which SUEZ is constantly seeking to make improvements, particularly to address the limited availability of land in urban areas. For 10 years, SUEZ’s research teams have been working to better understand and control how micro-organisms work within anaerobic digesters. Armed with the resulting knowledge, SUEZ has designed the Digelis®+ solution, which allows it to treat the same amount of sewage sludge in a facility almost twice as compact, i.e. with a volume around 40% smaller than a comparable facility. The technology is therefore particularly well suited to wastewater treatment plants in urban areas.
Making it easier to depackage food waste
SUEZ has acquired Vox, which has developed BioSV, a depackaging technology used to prepare food waste that is still in its packaging or that contains a large amount of impurities such as plastics and metal. The solution also improves the separation of non-digestible materials, cutting operating costs by reducing the amount of materials to be removed by 20-50%.
SUEZ’s research teams have made further innovations by developing a new waste digestion solution called Digelis® BHFW. This technology allows food waste to be digested alone or in combination with agricultural residues, without the addition of water, using a pre-treatment pro that naturally fluidifies waste, freeing up the water it contains. A pilot plant capable of processing 2,000 tonnes of waste per year will open in 2025 to showcase the expected benefits: preparing and digesting waste without added water, reducing the volume of digestate to be removed by 40% and cutting power consumption by 20% while increasing biogas production by 5%. It will be possible to apply this innovative method in new plants and integrate it into an existing anaerobic digestion chain.
Increasing the performance of anaerobic digesters using ai and digital technology
Anaerobic digestion is a sensitive biological process that can be disrupted by both internal and external factors such as the quality of incoming waste, the temperature and the presence of inhibitors. To help teams operating anaerobic digesters to monitor site conditions, SUEZ offers analytical and digital solutions that use predictive models and AI algorithms to help them take decisions, anticipate and limit risks that might reduce production, and ensure safe, optimised biogas production:
- MeMo®,a digital twin of the anaerobic digester that allows users to oversee the facility and provides recommendations to improve its performance based on predictive simulations
- SNAC®,a mini-laboratory connected to a web platform that analyses the digestate and alerts the operator if it detects issues with biological processes.
- Ir-SCAN®, a spectroscopic analysis method combined with an algorithm that produces a fingerprint for the material to be digested in only a few days, as opposed to 20-40 days for traditional analysis methods.
“Anaerobic digestion is not just a solution for processing organic material, it's a way of turning environmental challenges into genuine sustainability opportunities. It's the symbol of a circular economy that extracts value from each resource, resulting in a cleaner planet and greener energy.”
Gérard Téboul, Head of SUEZ's organic division
—
Some waste cannot be recycled, so thermal energy is recovered from it in energy recovery units (ERUs). That energy is then fed into urban and industrial heating networks or used to heat greenhouses. It can also be converted into electricity that is fed into the grid. This local, low-carbon energy source can partly replace fossil fuels, reducing greenhouse gas emissions and helping users to be more independent in energy terms.
Our innovation in action
SUEZ is a market-leader in France in terms of building ERUs, using the latest industrial and digital technologies such as computer vision to improve energy performance, reduce the carbon footprint and help integrate sites into their urban landscape and environment. In 2025, the Group now manages 31 ERUs in France, which produce low-carbon energy from 3.5 million tonnes of waste per year.
Since 1 January 2025, SUEZ and the Banque des Territoires have been helping waste processing authority Decoset to modernise the ERU in Bessières and rebuild a new plant in Toulouse to make energy from the residual waste of more than 1 million people in the Toulouse area. SUEZ’s project for Decoset sets a new standard in Europe. It includes the latest innovations to improve site performance and increase energy production, allowing the client to process waste while also increasing the community’s energy sovereignty.
Waste streams will be managed dynamically between the two sites: the waste will be directed more efficiently, depending on the needs of the heating networks supplied by the sites. Operational teams will use artificial intelligence and digital tools, providing them with a comprehensive view of waste processing in the community:
- QualiWaste, an artificial intelligence system that analyses images captured by cameras installed at the site to detect any non-conformity in the incoming waste and qualifies the waste by type (bulky waste that could cause blockages, recyclable waste and waste that must be rejected) in order to improve sorting quality.
- ValoVisio,a control solution that centralises operational data from facilities – incineration, energy production, fume treatment – and analyses it in real time. The aim is to anticipate the risk of failure by analysing problems and using predictive management, and to improve performance.
- The digital twin provides detailed plans of the plant, comprising a 3D spatial view and a set of technical data. In partnership with SAMP, the project uses an artificial intelligence system, recognising each item of equipment and infrastructure in the site. The digital twin ensures that entities working on the same site can easily share data with other participants.
80%
“ With this project, we are pursuing our vision of a resolutely future-facing community. By pooling and transforming our infrastructure, we are addressing the environmental issues of today while also anticipating the challenges of tomorrow. For localstakeholders, the project will reduce waste and generate more energy, as part of an approach that interacts with and is open to local ecosystems.”
Vincent Terrail-Novès, Chair of Decoset
—
France’s Energy Transition for Green Growth Act (Loi relative à la Transition Écologique pour une Croissance Verte or LTECV) set ambitious targets in terms of waste management and renewable energy generation: reducing waste storage by 50% by 2025 and increasing the percentage of renewables to 32% of gross final energy consumption in 2030.
In accordance with the waste hierarchy (reduce, recycle, recover, store), SUEZ helps businesses and local authorities to optimise their waste management and ensure they comply with current regulations. The Group has developed new local channels for recovering waste, such as solid recovered fuels (SRF), in which SUEZ is a pioneer in France, in order to generate sustainable and local energy.
Our innovation in action
Solid recovered fuels or SRFs are alternative fuels derived from non-recyclable commercial and household waste (wood conglomerate, paper and cardboard, soiled textiles) from waste disposal sites or directly from businesses. Using state-of-the-art sorting and crushing technologies, SUEZ transforms a wide variety of non-recyclable waste into high quality SRF. This waste is then converted into heat to supply industries or urban heating networks, as an alternative to fossil fuels.
SUEZ is helping a number of industrial operators in France to reduce their carbon footprint by turning waste into SRF. This includes sugar producer Tereos in the Hauts-de-France region. Its future SRF heat generation unit managed by SUEZ will replace 40% of the fossil gas consumption needed to run the Origny-Sainte-Benoite sugar refinery-distillery as of 2027. SUEZ is building a SRF unit for chemicals producer Novacarb (Humens) in the Grand Est region that will reduce the plant’s CO2 emissions by 60% as of the end of 2025.
In November 2024, the Group launched the first SRF unit in partnership with Vauban Infrastructure Partners in the industrial area of the Port of Le Havre. The plant produces 300 GWh of thermal energy a year from 90,000 tonnes of biomass and SRF to supply the Le Havre urban heating network and local manufacturing sites (such as the Yara plant and the Chevron plant). The SRF used for the BIOSYNERGY heat generation unit is prepared locally at the TriNergy site managed by SUEZ in Rogerville, a few kilometres from the plant, creating a short-loop waste recovery process.
50 000 T CO₂
—
“The BIOSYNERGY facility perfectly illustrates our desire to support the energy transition among industrial operators and local authorities by providing circular solutions. We are very proud of this innovative project, which responds to climate concerns (reducing GHGs) and economic concerns (controlling energy costs) on a local level, as well as allowing for energy sovereignty.”
Jean-Michel Kaleta, Infrastructure Director, SUEZ Recycling & Recovery France.
—
The European automotive industry is undergoing a major change in its business model due to the combined effect of climate change – requiring the transition to low-carbon energy – and increasing pressure on resources, with geopolitical tensions driving up production costs, as well as fiercer international competition. All these factors are redefining the sector’s rules of play. With 1.34 million vehicles produced in 2024, French automotive production has fallen to its lowest level since the 1960s.
To achieve this transformation, the automotive sector needs to evolve and adapt its model to the new challenges of the contemporary landscape. Speeding up the development of the circular economy in the automotive sector, or the “from car to car” economy, is not only an essential component of the environmental transition in this industry but also a means of achieving lasting growth and ensuring its industrial sovereignty.
Our innovation in action
Renault Group and SUEZ have decided to work together to address this challenge and make the circular economy a reality and a way of ensuring the resilience of the automotive industry. The two partners – which have worked together for many years in recycling metal waste and recovering end-of-life vehicles – took their collaboration up a notch in October 2024, with SUEZ acquiring a 20% stake in The Future Is NEUTRAL.
The Future is NEUTRAL is the first circular economy automotive company in Europe, serving all players in the automotive industry (manufacturers, equipment suppliers, retailers, insurers and consumers). Through its four subsidiaries (BCM, The Remakers, Gaia and Indra), the company provides circular economy solutions covering the entire automotive value chain, including design for recycling, reverse logistics, automotive waste management and closed loop recycling of materials for the production of new vehicles, or “from car to car”.
SUEZ offers years of know-how in waste management and is renowned for its expertise in industrial waste management, which it has used to help develop The Future is NEUTRAL:
- End-of-life vehicle management: collection, mass sorting, sorting and recovery
- Recycling of ferrous and non-ferrous metals
- Production of high quality secondary raw materials, reused to make new vehicle
- Development of a structured system for recycling electric vehicle batteries, including recovery of metals of strategic importance for the energy transition (copper, lithium, cobalt, nickel)
1,3 million
Galaxy The future is neutral
-BCM (Boone Comenor Metalimpex) collects, sorts and recovers automotive production offcuts and ensures that metal waste is recycled. In 2024, more than 1.8 million tonnes of metals were recycled (steel, aluminium) in Europe and Asia.
“SUEZ’s acquisition of a stake in The Future is NEUTRAL in partnership with us attests to the relevance of our longstanding presence in the automotive circular economy, which is now a key area of the market offering opportunities for growth. Our joint investment will enable us to offer a concrete response to the new challenges facing the automotive sector by ramping up our existing activities and creating new closed loop recycling solutions, from car to car.”
Luca de Meo, CEO of Renault Group
—
The development of new technologies related to mobility and renewable energies is leading to complex equipment (electric vehicle batteries) and composite materials (wind power, solar power) being brought to market, for which dismantling and recycling processes are currently being developed.
The need for equipment recycling is expected to gain pace between now and 2030 with the first generation of technologies reaching their end-of-life (on average 15 to 20 years). It is estimated that by 2025, an average of around 800 wind turbines will have to be dismantled each year in Europe, including 300 in France. This represents around 8,100 tonnes of blades to be recycled each year.
8100
Our innovation in action
The 500 m2 platform in Nanterre consists of five research centres, two test centres and one laboratory, with the aim of:
- Assessing processes for separating and preparing composite materials from solar panels and wind turbines
- Experimenting with optimised electric battery dismantling processes
- Testing waste classification and sorting technologies
- Developing and protecting “made in France” innovations
To this end, the teams at CIRSEE have been working since 2020 with other industrial partners and research centres on the ZEBRA (ZEro waste Blade ReseArch) project, headed up by the French technological research institute, IRT Jules Verne, to devise an eco-design approach for blades, which are the most complicated part of a wind turbine to recycle.
-LM Wind Power, for blades
-SUEZ, an expert in dismantling and waste treatment
-The CANOE R&D centre, a pioneer in composite materials recycling technologies
- ENGIE, for life cycle analysis of wind turbines
The SUEZ group has contributed to the ZEBRA project by providing its expertise in dismantling and crushing end-of-life wind turbine blades, a real step forward in blade recycling:
- It all starts with the strategy of dismantling blades according to the materials that make up the different areas (fibreglass or carbon, plastic resin, wood and polyester foam).
- The materials are then crushed and sorted using flotation, in which materials are separated according to their density relative to that of the medium used. For example, materials with a lower density than water float while others sink.
- Resins and fibreglass are then separated from other materials to be reused following a pyrolysis stage.