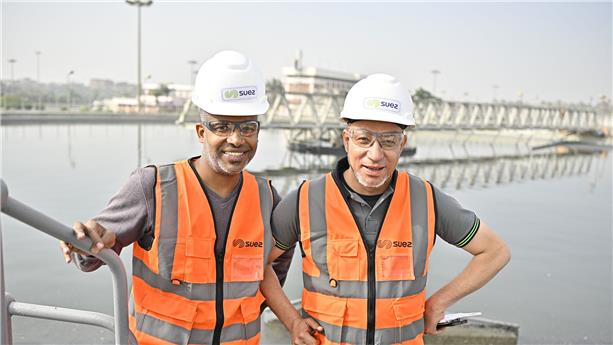
- Benefit from high-quality recycled plastics for your production processes
- Recycling plastic waste from all sectors of activity
- Contribute to the circular economy by avoiding using new fossil resources
Form is loading.
If the form does not load after a few seconds, please reload the page (CTRL + F5 or (or Cmd + Shift + R on Mac).
80 000
tons
of recycled plastics placed on the market
136 000
tons
of recycled plastic waste
4
plastic recycling plants
The use of recycled PET
The use of recycled PET saves virgin materials from non-renewable fossil resources that contribute to the environmental objectives of reducing the CO2 impact.
PET (polyethylene terephthalate) is the most widely used material to make packaging, especially beverage bottles. It is one of the most virtuous materials since it makes it possible to remake bottles from bottle waste. This is the principle of the circular economy.
The Single-Use Packaging Directive imposes a 25% recycled PET incorporation rate in beverage bottles from 2025.
Our coloured recycled PET flakes are compatible to make fibre and foam.
What are the different stages of plastic recycling?
According to the latest instructions in force, each user must sort all packaging, whether at home or even outside their home. This is an essential step in enabling the recycling of plastic packaging. Selective sorting bins are collected under the responsibility of local authorities, the contents of which are taken to a sorting centre for sorting.
Mixed packaging must be sorted by type of material. PET (polyethylene terephthalate) packaging, clear or coloured bottles and trays are
separated from the rest of the packaging waste in various stages. Our sorting centres have very advanced technologies where the latest innovations (artificial intelligence, optical sorting, invisible markers) work together to optimise sorting.
For example, with our Autodiag solution, a smart camera measures the quality of the waste collection in real time. Algorithms, fed with labelled images on the different types of waste, calculate the purity and homogeneity of the different qualities of materials produced.
We operate 2 PET recycling plants.
The first is located in Bayonne, in the heart of the Basque Country, the second in Limay in the Paris region.
The objective of recycling is to transform plastic waste into recycled plastic (flakes, granules) that can be used by plastics manufacturers using mechanical transformation technologies. It is done in several stages:
Sorting
Its objective is to separate the waste by polymer nature to keep only the PET. What for? Because plastics can be of a different nature and if they were recycled all together, we would get a material with bad properties, which would not replace virgin material. They could therefore not be reused in a new production cycle.
Sorting also eliminates unwanted materials such as metals, cardboard, etc.
Grinding
The purpose of grinding is to obtain particles that are all the same size, to facilitate the washing stages.
Washing and drying
PET bottles have contained liquids such as sugary sodas, oil, or thicker products such as ketchup or mayonnaise. To obtain quality recycled plastic, it is necessary to wash it hot with detergent to remove all residues.
Extrusion
Once dried, the flakes (the name given to the washed and dried shredded) are extruded (this is a manufacturing process) to obtain granules.
The extruder is equipped with a very fine filter that allows the last contaminants to be extracted.
Decontamination
To obtain food grade, you have to go even further and extract the impurities at the heart of the material. Decontamination involves leaving PET pellets in a vacuum reactor for several hours. The small molecules will be extracted from the recycled material.
Our control laboratory certifies the quality in accordance with our technical data sheets available on request, to guarantee the quality of each batch of recycled flakes / granules.
The use of recycled plastics saves resources, contributes to the reduction of the environmental impact of your products and has a positive impact on the climate and the environment.
We provide you with a carbon economy certificate that illustrates the potential contribution to reducing the carbon footprint of the products you manufacture.
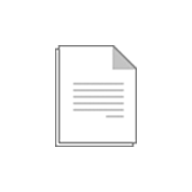
Brochure "A new life for plastic bottles"
The use of recycled LDPE
The use of recycled LDPE saves virgin materials from non-renewable fossil resources. This use contributes to the environmental objectives of reducing the CO2 impact.
LDPE (low-density polyethylene) is the most widely used material to make plastic films, whether in secondary packaging for pallets or for films for agriculture. It is one of the most virtuous materials, since it allows films to be remade from film waste. This is the principle of the circular economy.
The quality of our clear LDPE granules allows you to meet your clear or colourable film manufacturing needs.
The quality of our black LDPE granules allows you to meet your dark film manufacturing needs.
Our range of recycled LDPE offers a wide range of MFIs (Melt Flow Index) that can be adapted to other applications:
- Auto Parts
- Tubes and pipes
- Cable Jackets
- Agricultural films, industrial films...
- Bags
What are the different stages?
Through its agencies, we offer our industrial, commercial and mass distribution customers the collection of transparent plastic films. Once collected, they are compacted to optimise transport.
Adivalor, a voluntary and collective initiative of the entire profession for the collection and recycling of agricultural plastic waste, organises the collection and delivery of films to our recycling site.
We operate a LDPE recycling plant located in Landemont, near Nantes, which includes several recycling lines dedicated to agricultural films on one side and industrial films on the other. The objective of recycling is to transform plastic waste into recycled plastic that can be used by plastics manufacturers, using mechanical transformation technologies. It is done in several stages:
Sorting
Its objective is to separate plastic waste by polymer nature to keep only LDPE
Plastic waste can be of a different nature and if it were recycled all together, we would get a material with bad properties, which would not replace virgin material. They could therefore not be reused in a new production cycle.
Sorting also eliminates unwanted materials such as metals, cardboard, etc.
Grinding
The objective of grinding is to obtain particles that are all the same size to facilitate the washing steps.
Washing and drying
Agricultural LDPE films are loaded with soil and sand that must be perfectly cleaned to keep only the plastic. 3 steps of cold washing are required to ensure high quality.
LDPE films from industry or trade often contain tape or labels. It is necessary to wash them hot to remove all these impurities.
Extrusion
Once dried, the flakes (the name given to the shredded film that has been washed and dried) are extruded (this is a manufacturing process) to obtain granules.
The extruder is equipped with a very fine filter that allows the last contaminants to be extracted.
Our control laboratory certifies the quality in accordance with our technical data sheets available on request, to guarantee the quality of each batch of recycled pellets.
The use of recycled plastics saves resources, contributes to the reduction of the environmental impact of your products, and has a positive impact on the climate and the environment. We provide you with a carbon saving certificate that illustrates the potential contribution to reducing the carbon footprint of the products you manufacture.
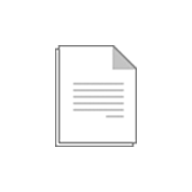
Brochure "Recycling agricultural and industrial LDPE films for raw materials"
The use of recycled PVC
The use of recycled PVC saves virgin materials from non-renewable fossil resources. This use contributes to climate and environmental objectives by reducing the CO2 impact.
PVC (Polyvinyl chloride) is the most widely used material in the construction industry: pipes, tubes, profiles to make windows, etc. It is one of the most virtuous plastic materials, since it makes it possible to remake tubes from waste tubes and window profiles from carpenters' production scraps. This is the principle of the circular economy.
The quality of our custom-dyable PVC granules allows you to meet your CSTB regulatory requirements for reincorporation into new profiles.
Our micronised PVC can be used in tubes, multilayer pipes and decking boards.
What are the different stages?
We provide you with storage containers that we collect once filled with rigid PVC scraps.
On request, we can arrange for the collection of your waste pipes and tubes.
We operate a PVC recycling plant located in Vernie, near Le Mans, which includes several recycling lines dedicated to building waste.
The objective of recycling is to transform plastic waste into recycled plastic that can be used by plastics manufacturers using mechanical transformation technologies. It is done in several stages:
Grinding
The aim of grinding is to obtain particles that are all the same size.
Extrusion
After grinding, the shredded material is extruded (this is a manufacturing process) to obtain granules.
The extruder is equipped with a very fine filter that allows contaminants to be extracted.
Micronisation
After grinding, the waste PVC pipes and tubes are reduced to powder after being placed in a microniser.
Our control laboratory certifies the quality in accordance with our technical data sheets available on request, to guarantee the quality of each batch of recycled powder/granules.
The use of recycled plastics saves resources, contributes to the reduction of the environmental impact of your products, and has a positive impact on the climate and the environment.
We provide you with a carbon saving certificate that illustrates the potential contribution to reducing the carbon footprint of the products you manufacture.
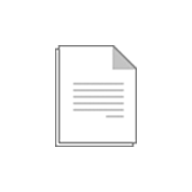
Our brochure "PVC recycling, an asset for manufacturers"
Do you have specific needs for plastics recycling? Contact us, we will study your needs.
We have created Plast'lab®, a laboratory dedicated to the recycling of plastics, which is based on the development of partnerships with plastic-consuming industries, by meeting precise specifications.
Plast'lab® makes it possible to analyse, characterise and test recycled plastics to formulate new ranges of qualitative plastics. The aim is to meet your requirements (impact resistance, bending, rheology, heat resistance, etc.) and to anticipate the needs of tomorrow.
PLAST’lab® Collecting, sorting, and recycling of plastic waste - SUEZ
Credit: SUEZ group
They trust us
A trusted, solid and long-lasting partnership with ALMA sources
Number 1 in France among water bottlers thanks to its Cristaline brand, ALMA Sources is also number 1 for the recycling of PET (polyethylene terephthalate) bottles. As early as 2009, many bottles from Alma sources incorporated recycled plastic. A pioneer in bottle recycling, we supply Sources Alma with clear PET flakes suitable for food contact from our factory in Bayonne. Our relationship with Les Sources Alma is more than a commercial relationship but a true partnership of trust where we support each development project of Les Sources Alma.
Frequently Asked Questions
There are 4 conditions for recycling an object containing plastic:
- It must be sorted, that is to say that there must be an organised system for collecting this object. For example, plastic packaging is collected in the yellow bin or at voluntary drop-off points.
- It must be sorted, i.e. the material that makes up this object must be targeted in the sorting centre. PET, for example, will be sorted, while PLA will not.
- It must be regenerated, that is to say that there must be factories that can transform plastic waste into recycled plastic used by an industrialist.
- It has to be used, that is to say that there has to be a market for this recycled material, that there are customers who buy this recycled plastic.
Plastics that cannot be recycled are those that do not meet the 4 conditions of collection, sorting, regeneration and use.
These include:
- Multilayer plastics
- Plastics containing substances that are banned today because they were put on the market a very long time ago.
There are two main families of plastic recycling:
- Mechanical recycling. With mechanical techniques such as sorting, shredding, washing, extrusion, plastic waste is transformed into recycled plastics that can be used by the plastics industry. The core of the plastic is not modified, it is not possible to change the colour, to extract substances.
- Chemical recycling. With chemical techniques, such as dissolution with solvents, depolymerisation, the use of catalysts, reactors, distillation columns, plastic waste is transformed into recycled plastics that can be used by the plastics industry. The core of the material is washed, purified, it is possible to obtain a recycled plastic equivalent to virgin, colorless, odorless, food-grade plastic.
The objective of recycled plastic is to replace virgin, petroleum or agronomic plastic in order to save resources. Every ton of recycled plastic used is a ton of virgin plastic saved. With recycled plastic, it is therefore possible to do the same thing as with virgin plastic: packaging, car parts, cable sheaths, plastic bags, tubes and pipes, windows...