Oxidation
Direct Oxidation Systems
Recuperative Thermal Oxidation System
In recuperative systems, volatile organic compounds (VOCs) can be converted to carbon dioxide and water vapor by thermal oxidation at temperatures above 750 ° C.
It consists of an integral primary shell and a tube heat exchanger to preheat the incoming polluted air using the high temperature air leaving the equipment.
When the VOC level is significant, the heat released during the oxidation of the VOCs will also be recovered, improving the system profitability.
A primary heat exchanger can recover up to 70% of the heat contributed by the burner or released during the oxidation process by preheating the inlet exhaust stream, reducing the support fuel required by the burner to maintain the required oxidation temperature.
They are a simple and cost-effective means of destroying VOCs when the input concentration is relatively high, in particular, when heat can be usefully recovered for other processes.
Secondary heat exchangers can also be used to recover heat as a utility for other energy requirements.
Regenerative Thermal Oxidation Systems
Regenerative thermal oxidation systems can be used in many applications. Its entire dynamic heat exchange system can be used to produce thermal efficiencies of up to 98%. This high level of thermal efficiency minimizes the need for additional backup fuel and, in many applications, allows the RTO (Regenerative Thermal Oxidizer) to operate in an autothermal way, without the addition of any fuel, in flameless mode.
The principle of the RTO is simple. The contaminated stream is introduced into the equipment through a heated ceramic bed where it absorbs heat prior to combustion. Hot volatile gases enter the combustion chamber where they oxidize (typically 800°-900°C) in an exothermic reaction that releases additional energy into the system. If there is enough heat generated by internal heat recovery and exothermic reaction, the burner will shut down. In this flameless autothermal condition, the combustion chamber temperature will be maintained without supporting fuel.
The gas is kept at the design temperature in the combustion chamber for the required residence time. The clean gas exits through a second bed of ceramic medium where it gives up its heat, leaving the equipment only slightly warmer than it entered. At the end of this cycle, the outlet bed of the equipment is hot and the inlet bed is now cooler. Therefore, the cycle is periodically reversed to maintain equilibrium and maintain the recovered heat within the oxidizing system.
Rotary Concentration System
A roto-concentrator system uses a combination of adsorption and thermal or catalytic technology. These equipments are designed for the treatment of high flow emissions and, a priori, low concentrations.
A concentrator, by itself, does not destroy VOCs, it simply concentrates them for more cost-effective destruction in a catalytic or thermal oxidation system.
Our company provides rotary concentrators that use activated carbon or zeolite as an adsorbent medium to remove VOCs from the main process exhaust stream prior to discharge to the atmosphere. In a concentrator system, the main airflow passes through the rotating concentrator wheel where VOCs are absorbed onto the carbon or zeolite surface, allowing the clean air to be discharged to the atmosphere. At the same time, a second and much smaller flow of hot air passes through a separate section of the rotating wheel in the opposite direction. This smaller stream desorbs the VOCs from the surface of the wheel ready for destruction into a catalytic or thermal oxidant.
The total effect is the concentration of the solvent in the main air stream into a much smaller air stream that can be cost-effectively destroyed in an oxidant. Concentration ratios of 8 to 15 times are normal and this will typically allow the oxidant to function autothermally and the excess heat generated in the oxidation system will be used to heat the desorption air.
SUEZ Air & Climate works together with the manufacturing company EIS (Environmental Integrated Solutions Ltd) in the sale of this equipment in Spain.
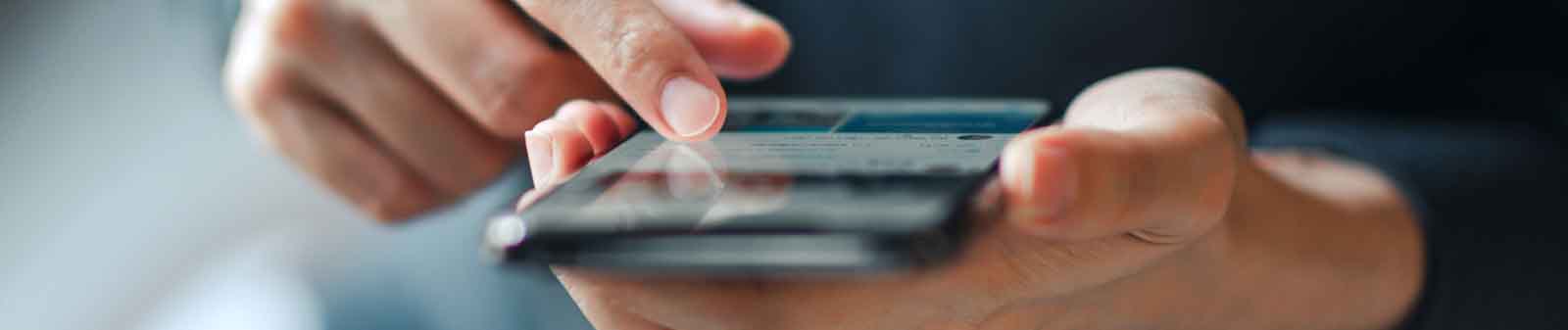