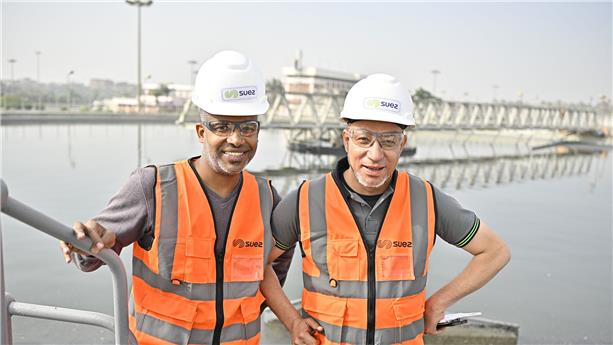
Artificial intelligence and robotics to enhance performance
In particular, artificial intelligence is enabling us to make more informed decisions by analysing and processing large volumes of data. With high-performance algorithms and large volume of Data, we can anticipate customers’ needs, improve our processes and reduce operating costs.
Robotics, meanwhile, offers numerous potential ways of automating repetitive and dangerous tasks, increasing productivity and improving safety at our sites.
By adopting these technologies, we can remain competitive in the global market and position ourselves at the leading edge of innovation in water and waste management.
We are allocating a large number of resources to those initiatives:
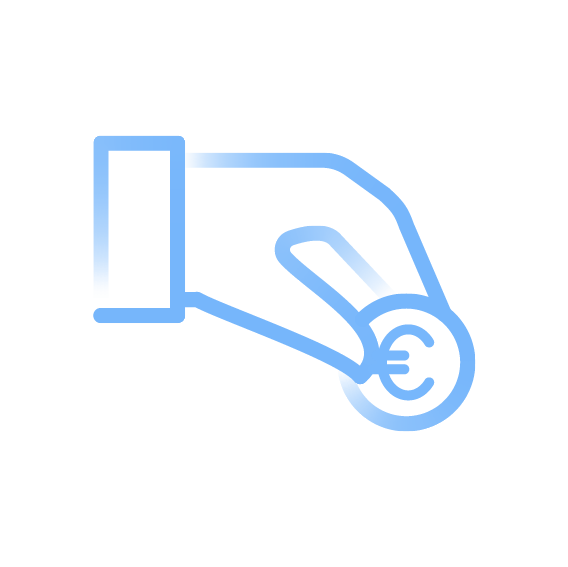
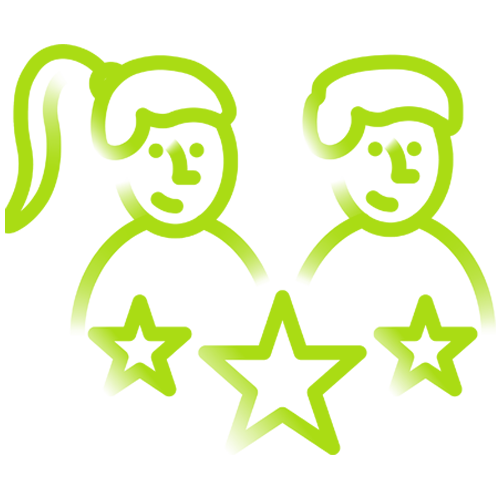
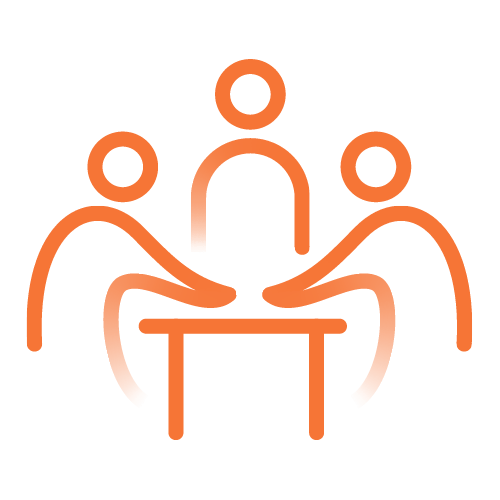
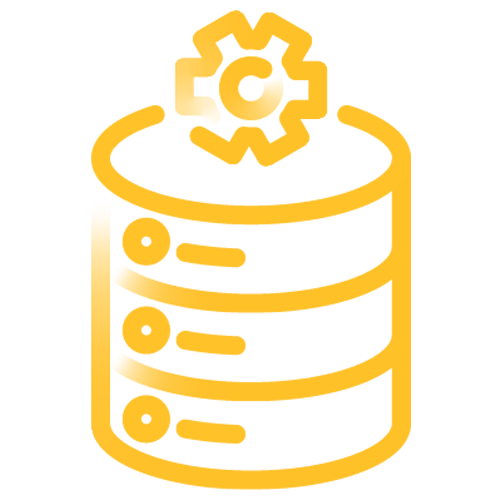
Our ability to use these technologies in a responsible and efficient way enables us to meet our customers’ complex needs, while contributing to a future that is sustainable for all.
Our approach fits perfectly with our new corporate purpose focusing on resource stewardship and the fight against climate change.
Artificial intelligence to improve water stewardship
< 5%
At SUEZ, we are pioneers in the deployment and operation of AI-based digital solutions to improve the performance of water supply systems. We use smart sensors to collect data, Hhpervision platforms to check that our customers’ facilities are operating correctly and algorithms to process data. This allows them to see the condition of the network, anticipate the risk of breakage, and detect leaks in real time.
Treasures in our trash: artificial intelligence and waste recognition
Maximizing waste recovery by ensuring that waste streams are directed to the appropriate facilities is a key priority in waste management.